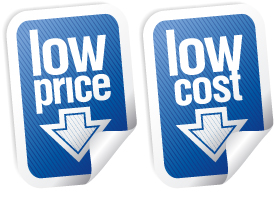 |
Cost reduction for implemented products can be realized by:
- Redesign – The classic value engineering approach involves re-design to reduce parts count, simplify assembly/test, and use lower cost parts. This method, often called “cost avoidance”, yields the biggest result when initiated at the beginning of the project. Avoiding cost before the first revenue ship (FRS) is easier than decreasing cost afterwards.
- Existing component cost – The fastest, least intrusive way to decrease product cost is to decrease how much you are paying for parts. On common components this may be done by renegotiation, or sourcing through a different vendor.
- Component substitution – The second fastest method is to substitute components. In the best case scenario, an equivalent part with lower cost replaces an existing component. More likely, an existing part is replaced by a lower quality component with lower cost but that still meets design and quality assurance goals.
- Re-sourcing/Out-sourcing – Custom parts and manufacturing sites can be re-sourced or out-sourced to a lower cost producer
- De-featuring – Another fast method of lowering cost is to examine what features and options are really valued by customers and offer only those which make economic sense.
|